What Is Asbestos Awareness Training?
Asbestos awareness training is a type of mandatory Health and Safety Awareness Training that educates workers about the dangers of asbestos exposure in the workplace, including how to identify where and when asbestos was used and what to do if it is found in their workplace. The awareness training usually consists of an initial information session for new employees as well as refresher training for all workers on a yearly basis. The training outlines the potential health risks associated with asbestos exposure, as well as the Occupational Safety and Health Administration (OSHA) standards for preventing exposure to airborne fibers released from asbestos containing material during activities such as demolition or remodeling .
Although many uses of asbestos have been banned for decades, there are still thousands of older structures that contain asbestos materials in their roofs, walls, ceilings and floors that could be disturbed during renovation, repair or maintenance activities, exposing unsuspecting workers to significant amounts of asbestos fibers. Even minimal exposure to asbestos can lead to long-term, often fatal, diseases such as malignant mesothelioma. Because of the severe health risks associated with exposure to asbestos, OSHA has strict requirements when it comes to asbestos awareness training.
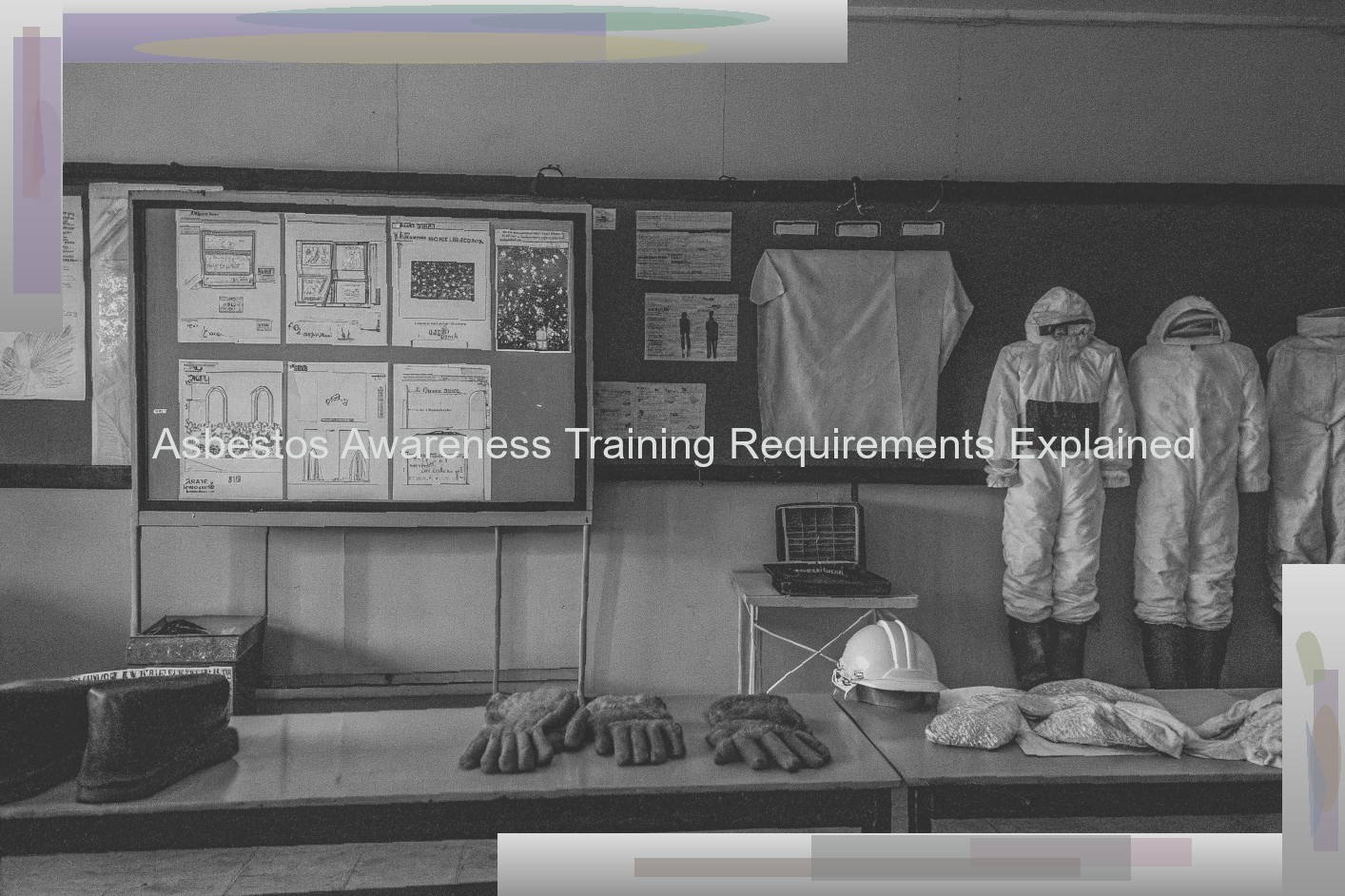
Who Requires Asbestos Awareness Training?
In 2013, the Environmental Protection Agency (EPA) updated its requirements for "Asbestos in Construction" under the National Emission Standards for Hazardous Air Pollutants (NESHAPs). This update increased the likelihood of regular jobs and activities involving disturbation of materials containing asbestos that all employers and employees need to consider.
As a point of reference, the EPA states that any renovation or demolition work that involves disturbing materials containing asbestos is "demolition" and must be performed in compliance with the standards set forth by the NESHAPs.
These requirements apply to "any facility being demolished on or after March 7, 2011" and "to any building demolitions on [or] after May 2, 2013…" This effectively means that any moderate to high risk construction job needs to involve trained employees.
Below is a short list of the types of workers typically in need of asbestos awareness training:
- Construction workers
- Demolition workers
- Shipyard employees
- Workers who maintain and inspect building systems
- Roofers
- Plumbers
- HVAC technicians
- Maintenance workers
- Painters
- Plumbers
- Pipefitters
Additionally, there are some non-construction workers that may require training if their jobs include possible exposure to asbestos, such as:
- Health care professionals
- Emergency responders
- Industrial hygienists
- Safety officers
- Laboratory workers
However, this list contains only those workers and workplaces that frequently involve exposure – in some cases, exposure to asbestos is necessary for an industry, in others, it is an intermittent risk. Either way, even if those potentially exposed workers do not legally need asbestos awareness training, acquiring training can still be in their best interest.
Companies who choose to involve their non-legally required employees in this type of training can better equip their employees to protect themselves from asbestos exposure, and ensures that employees are thinking ahead and actively protecting themselves as they continue to work in such a field.
Asbestos Training Regulations
At the national level, professionalism derives, in large part, from the Occupational Safety and Health Administration (OSHA) standards, which set forth the procedures, requirements, and expectations for safe asbestos-handling procedures. OSHA requires that both employees and employers have a certain knowledge of the roles and responsibilities they each have for ensuring the safety of the work environment, including understanding the training requirements established by OSHA. The EPA also has training protocol that must be adhered to by commercial asbestos abatement firms and by state and local governments. However, while both OSHA and the EPA regulate asbestos at the federal level, each state has its own regulations on how to contain and remove asbestos, or if it is simply necessary to seal the substance. These state laws are parity to, and may be stricter than, the federal regulations.
Beyond OSHA and EPA, the federal government has passed the Asbestos Hazard Emergency Response Act (AHERA), which is situated at 40 CFR part 763. This regulation applies to all public and non-profit elementary and secondary school systems, and establishes training requirements for maintenance and custodial staff who may come in contact with asbestos during the course of their work. AHERA requires the training of these individuals so that they are capable of identifying various forms of asbestos that may be present in the school building, and to notify the proper school official of any asbestos-related information. Additionally, AHERA mandates that all school district personnel receive refresher courses every three years to maintain currency in the rules and procedures for dealing with asbestos, which is where the legal knowledge comes in to play.
Guidelines at the international level primarily come from the World Health Organization (WHO), a specialized agency of the United Nations, who aims to develop a more standardized approach to the handling of asbestos. While WHO has undertaken to reduce asbestos exposure by "assisting countries to prepare national asbestos bans," they have yet to release any standard training protocols, leaving it to each country’s sole discretion to design what type of instructional material abatement workers and their supervisors must complete. Ultimately, for any jurisdiction − city, statewide, or federal − it will be interesting to see whether the laws and regulations will evolve, as they have internationally for WHO, and congeal over time to create one cohesive set of standards.
Components of a Good Asbestos Training Session
The effective asbestos awareness training programs address essential, company and site specific items. Whereas there is no "one-size-fits-all" training program there are specific components that are common to the most effective asbestos training programs.
Personnel Qualifications
One common component of the most effective asbestos training programs is the formal qualification of the personnel delivering the asbestos training. While there are no mandatory qualification requirements, the credibility of the trainer is enhanced when he or she has a background in industrial hygiene or environmental permitting issues. One method by which to validate the credentials of the trainer is requiring the trainer to submit their qualifications to the training program developer prior to performing the training session.
Generally, operators are responsible for ensuring the air-tightness of structures. That responsibility is delegated to asbestos workers through the removal of asbestos on those structures. Thus, those working with asbestos frequently should understand the unique nature of asbestos-containing building materials (ACBMS), and the potential consequences associated with improper handling of those materials. Moreover, proper training of non-asbestos workers is required per OSHA, EPA, and other regulations.
Training Delivery
Beyond the personnel delivering the asbestos training, the effectiveness of the training is also determined by the way in which training is delivered. As discussed above, asbestos awareness training must be site specific and training delivery should be flexible enough to ensure it is applicable in the field. The most effective training programs offer both field and classroom training (on a regular basis). Additionally, the training should be taught in small groups (e.g., less than 15) to encourage discussion and questions/answers.
Training Content
While training individuals to become certified asbestos workers is a volunteer effort of numerous trade organizations, municipalities, and schools, both OSHA and EPA have specific requirements as to what must be included in a general asbestos awareness training program. The essential topics of an asbestos awareness training program include:
In addition to including the mandatory topics identified above, training that provides more than the mandatory coverage of the topics, also improves awareness of workplace safety practices.
Length and Frequency of Asbestos Training
As discussed above, the EPA does not dictate the duration or frequency of training. Instead, the six-hour training period included in the EPA website is a recommended average duration and can be adjusted based on a number of factors. Asbestos Awareness training should be customized to meet site specific needs and to correlate to specific operations. It is important to note, that although the EPA does not require refresher training, many states do require refresher training on a set schedule . In Illinois, for example, the Asbestos Abatement Act of 1983 requires reduction of air contaminants emitted into the environment from a building during removal of asbestos and grants the Illinois EPA plenary and exclusive power to prescribe performance and control standards including the requirement of refresher training. Accordingly, Illinois has adopted the following training schedule: [That said,] [i]t is important to point out that the EPA does not require refresher training, however, many states do require refresher training at specified intervals from 6 months to 12 months depending upon the state.
Asbestos Training Provider Selection
I have attended many continuing education courses over the years, and I can tell you that they are not all created equal. Some seem stick more or less to the subject matter, while others get off track-way off track-into what’s happening on Dancing with the Stars or the alleged evils of this or that device. While this may be entertaining for the participants, it usually doesn’t leave much room for adequate coverage of the subject for which the provider is licensed.
As an attorney and one who takes education very seriously (I usually obtain far more than is legally required), I have come to realize that in assessing a training program, a participant should begin by looking at the key people involved with the program. Searching for a qualified instructor, looking at their credentials, and researching the company offering the program are all good starting points. In addition, calling some of the people that have previously attended the program can be very helpful.
When a school or organization goes through the certification process, there are actually three sets of inspections, one by the state, one by the EPA and one by the discipline or credentialing institution. Not only is a school inspected by the EPA, but its records are inspected as well, including records regarding attendance and certification. On top of that, an EPA representative will actually show up at the school at and often make unannounced visits to review a school’s program and documents. This is typically followed up by a mock inspection looking at the school’s program. If you don’t have your house in order, the EPA can suspend your certification. Continuing education is only beneficial if the provider is certified and is actually providing the necessary information.
When you are considering taking an asbestos awareness class, in addition to these inspections, you should also do your own research. I am pleased to recommend Rosen & Associates, which offers classes to individuals seeking federal or state credentials and is a certified EPA school.
Asbestos Training Implementation Challenges
A number of organizations face difficulties with implementing training, which range from lack of resources and time to employee engagement, compliance, and enforcement. Let’s take a look at some ways to work around these issues.
Time
An online training solution may help conserve time in that an employee may complete training when time permits — this facility is now built into most of the modern online training authoring systems. A good online training platform will track all key metrics such as completion rates and scores but the downside is that quarterly online refresher training is less effective than more frequent, shorter training units. We feel that an hour-long refresher every quarter is not as effective as 10-minutes every month or once every two weeks.
Resources
Most web-based systems were developed over 10 years ago when regulatory agencies did not understand what an LMS was and so did not put any controls in place. The result is that anyone with a credit card could purchase a system without an understanding of not only what the system actually does but that the standards do not include criteria for the LMS. Gaps can be created by easy access to training materials, especially if the material is easily duplicated, downloaded, and forwarded to others.
Engagement
Staff engagement in an online system can be difficult, particularly if the company has a good in-house quarterly rollout program. Deployments must be a combination of online/distance learning, video, classroom instruction, no more than an hour per quarter, and emails or newsletters. Different media and methods increase effectiveness.
Compliance
We have eight different issues to cover in our SIS – site specific inspections, annual audits, general awareness, training, notification, recordkeeping, 2520 certification, and labelling – that all have specific timeframes (i.e., site specific inspections must be performed every 2 years, annually for Type 1&2 asbestos). Training and refresher training is required yearly by law but generally isn’t effective. It should be supplemented by site specific inspections and training of those workers who need to know more.
Asbestos Training Legal Implications and Penalties
Failing to meet training requirements for asbestos awareness can have serious legal ramifications for organizations. In addition to the direct costs of providing proper training, non-compliance could lead to significant penalties. The Occupational Safety and Health Administration (OSHA) has the authority to issue citations and fines to organizations that fail to provide required training or to carry out adequate record-keeping.
A Citation is a finding that an employer has violated a mandatory OSHA standard or rule. An organization may receive a Citation for the first occurrence of a violation, for the second or third occurrence, etc. These Citations will carry with them a minimum Penalty . This Penalty is calculated by multiplying the $ value listed in the adjusted penalty tables ($14,502 in 2019), by the Serious level of the individual violation.
Penalties are then modified based on the organizations Good Faith, Size and History, to adjust for things like their number of years of receiving a Citation, their size, the fact that they may have already taken numerous steps to reduce the level of Penalty, etc.
Penalties are capped at a maximum of $132,598 for serious violations. Repeat and Willful Citations can be significantly higher as the initial Cap of $132,598 is adjusted to $132,598 per employee potentially exposed to a hazard. Therefore, an organization could receive Penalties for a Violations of up to $13 million (without Good Faith, Size or History modifications).
No Responses